The Role of VFD in HVAC Water Pump Energy Savings
With the continuous improvement of our people’s living standards, the HVAC system has entered the hotels, restaurants, industrial and mining enterprises, office buildings and other fields. HVAC system design is first based on outdoor meteorological parameters and indoor air conditioning design parameters to calculate the cooling load, according to the characteristics of the partition structure, according to the product samples to select the appropriate equipment, combined into a system. However, the vast majority of the time the HVAC system is working under less than full load, resulting in a great waste of electrical energy. With the development of modern advanced science and technology, variable frequency drives (VFDs) have been widely used in the HVAC pump energy efficiency retrofit industry. The HVAC system, using VFD control technology, in the case of low cost, can achieve average power savings of up to 20% or more.
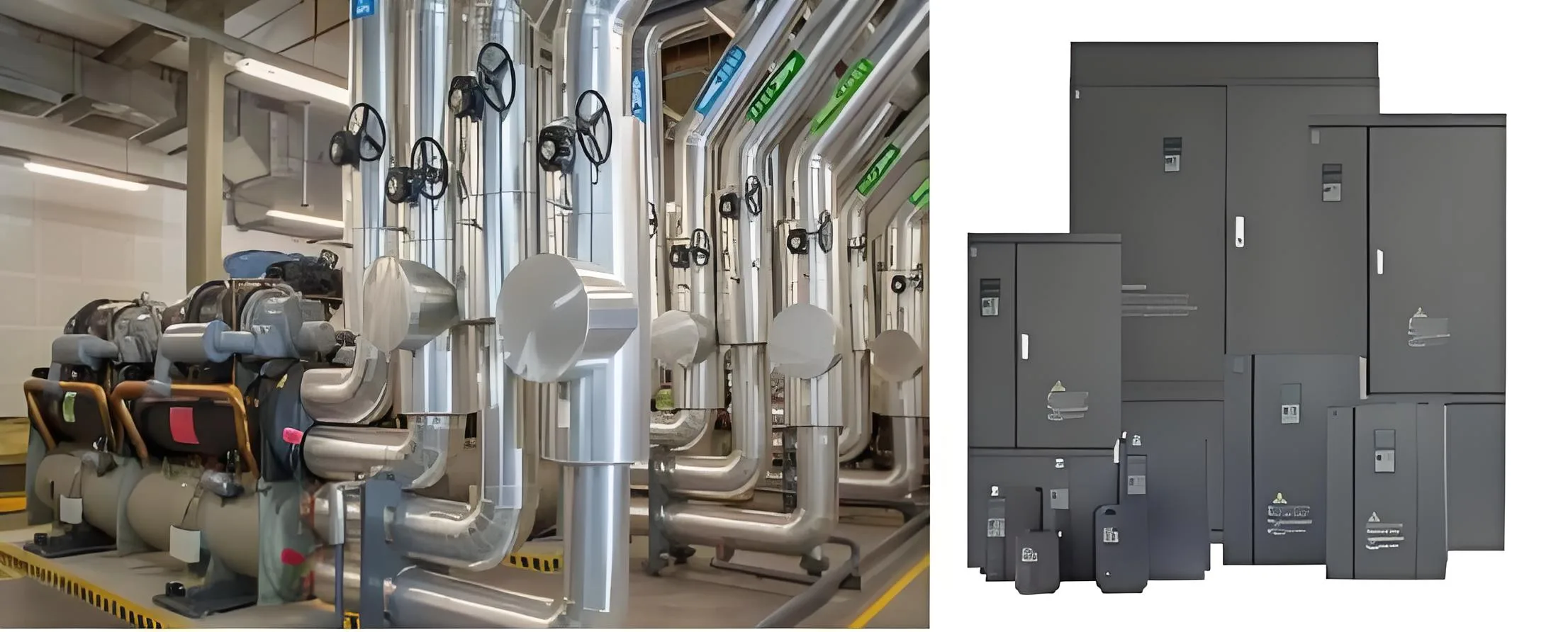
If the use of variable frequency control, energy transfer and transportation link control for variable water volume (VWV) and variable air volume (VAV), so that the transfer and transportation coupling and to achieve the ideal temperature displacement, the power is only 30 to 60% of other control systems, and energy efficiency is a double effect, because of the demand for the refrigeration host energy consumption at the same time down. Host using VFD energy-saving control, to maintain the design conditions of the refrigerant movement of physical quantities (such as temperature difference, pressure, etc.) changes in energy saving than other ways to adjust the load is obvious, such as York (YORK) YT-type centrifugal chiller, configured with VFD units in part of the load under the energy-efficiency ratio can be reduced to 0.2kw/cold tons, can be seen in the HVAC system the application of VFD control mode has very broad prospects.
In the past, due to price reasons, in the HVAC system the application of VFD technology was more difficult to promote. Variable frequency drive technology, computer automation control technology is very mature today, with this technology combined with HVAC expertise, it is not a high-priced technology, in the low-power HVAC application in the economy can be afforded, in the HVAC system should not be a problem:
- HVAC system running time is longer, energy efficiency issues are more prominent
- VFD control in the whole system accounts for a small proportion of the cost
- The larger the capacity of the VFD controller, the lower the unit price per kilowatt of power
HVAC system using variable frequency drives is feasible, its investment recovery is generally in 6 to 12 months, in order to VFD controller service life of 10 years, its net income is 10 times the amount of investment.
HVAC VFD energy efficiency principle
Refrigerant through the compressor will be compressed into a liquid refrigerant sent to the evaporator and chilled water for heat exchange, the chilled water cooling, chilled water pump will be sent to the chilled water cooling coils of the fan outlet, the fan blowing cold air to achieve the purpose of cooling. The evaporated refrigerant releases heat in the condenser, exchanges heat with the cooling circulating water, and the condenser water pump brings the cooling water with heat to the cooling tower where the tower fan sprays the cooling, and exchanges heat with the atmosphere, and distributes the heat to the atmosphere.
The old operating system is “star-delta conversion starting” full-voltage operation, at this time the HVAC unit works under full load, the system cannot be started smoothly when starting the motor, the impact on the power grid is large when starting, long time and frequent starting will result in the insulation of the motor decreasing, the motor temperature is too high, in the process of operation, cannot effectively adjust the temperature of the cooling water according to wards and office building demand. In the process of operation, the temperature cannot be effectively adjusted according to the needs of the wards and office buildings, but only a large number of industrial frequency feeding, which will inevitably cause a waste of energy.
And through the VFD retrofit, according to the room’s cooling and heating needs automatically adjust the flow rate of the chilled water pumps and condenser water pumps to achieve the purpose of energy saving and consumption reduction.
(1) Due to the current condenser water circulating pump running at industrial full-load frequency, during early and late cooling cycles, the ambient temperature is low, the condenser return water temperature is low, causing lithium bromide crystallization, resulting in reduced efficiency or protection. After adopting VFD constant temperature difference control, the return water temperature is effectively controlled, which will greatly improve the efficiency of the HVAC unit and achieve the purpose of energy efficiency.
(2) Because the chilled water circulating pump is also operating at full capacity at work frequency and cannot automatically adjust the flow rate according to the requirements of the indoor temperature, the VFD retrofitted chilled water pump can automatically adjust flow rate based on the outdoor and indoor temperature, improving efficiency and achieving the energy saving goal.
(3) Reduce the impact on the power supply and system when the HVAC unit starts and stops. Due to the greater power of the circulating water pump, the impact on the power grid is greater when the pump is started/stopped at industrial frequency, affecting the operation of other equipment. VFD control allows soft start and stop, the current is less than the rated current, reducing grid impact.Reduce the water hammer effect of circulating water when stopping the pump. Due to VFD soft stop, the stopping process can be controlled, eliminating the water hammer impact on the HVAC pipe network.
(4) Reduce the failure rate of equipment:With VFD control, the circulating water pump mostly works below rated power, which significantly reduces the equipment failure rate and maintenance cost.
(5) Improve the degree of automation of the equipment:Achieve overload and overcurrent protection for chillers, automatic temperature control of condenser and chilled water, ensuring safe system operation.
In summary, applying variable frequency drives in HVAC circulating water pumps delivers significant economic benefits, making VFD retrofitting essential for energy efficiency.
HVAC VFD system design
- Condenser water pump VFD retrofit design
- Professional VFD control mode – constant temperature difference control
- VFD energy saving control principle
- Variable frequency control system adjusts the pump speed based on return/outlet water temperature difference, ensuring stable cooling water temperature delta.
- Pump power consumption is proportional to the cube of speed: P ∝ n³ – cooling pump speed
Control system functions
- Condenser/return water temperature detection and display
- Automatic constant temperature difference control
- Energy saving rate: up to 20%+
- Running/standby pump auto switching
- Over-temperature/under-pressure alarm
- Condenser water pump overload protection
- Chilled water pump VFD retrofit
- Closed-loop VFD control mode
Chilled water pump closed-loop control
Based on maintaining chilled water supply to terminal equipment, determine a minimum working frequency for the VFD-controlled chilled pump, set it as the lower limit, and use a return water temperature sensor to adjust VFD output via a temperature controller. When return temperature > setpoint, frequency increases.
Same as above, but when return water temperature < setpoint, frequency increases; when it’s higher, VFD output decreases.
It shows that the pump’s power usage is directly proportional to the chiller’s cooling capacity: P ∝ Q – cooling capacity.
Control system functions
- Variable frequency drive (VFDs): maximizes motor power factor and efficiency
- Temperature/pressure transmitters: high precision for monitoring the network
- Control instrumentation: high control accuracy, low failure rate
- Specialized HVAC control system: good operability, remote monitoring
- Low-voltage components: breakers, contactors, relays for safety
Today, VFDs applied in HVAC pumps are favored by the industry. Our EV series variable frequency drives deliver exceptional energy savings, reliable performance, and extended service life of motors, contactors, mechanical components, valves, and piping—bringing greater economic benefits to HVAC operators.
For more VFD energy saving solutions, contact us at sales@vfd-drives.com.